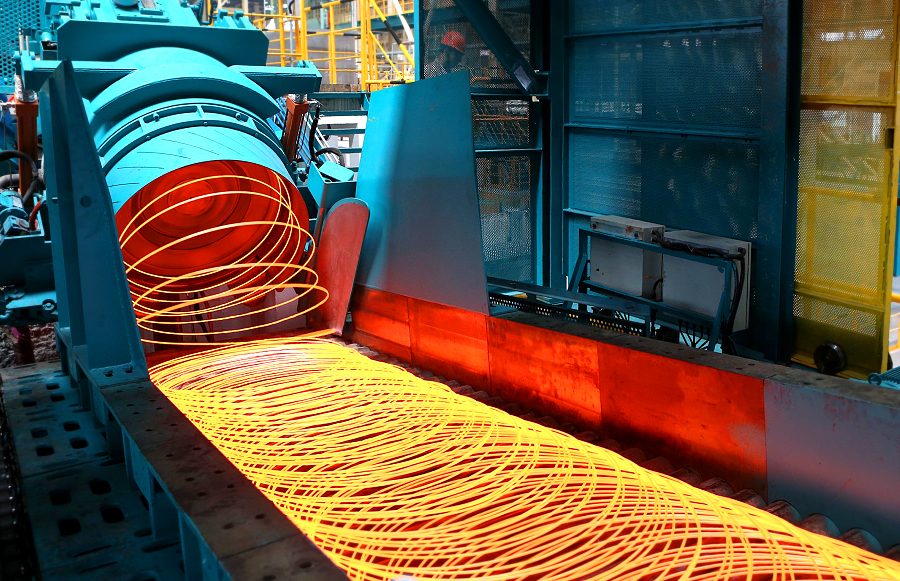
50,000-300,000 tons of rebar and wire rod production line is the most popular steel production line, whose finished product size is 8-32mm, and the final product can be ordinary carbon steel, high-quality carbon structural steel, low alloy steel; the designed annual production capacity is 50,000-300,000 tons, and the maximum line speed of finishing mill is 5 -16m/s.
The billet of the continuous rolling production line is 100×100–150×150 continuous casting billet and the length is 3000mm–6000mm, all of which are provided by the internal steel-making continuous casting workshop of the company.
The new continuous rolling production line has a new regenerative push-type steel heating furnace. The fuel is blast furnace gas, and the air is preheated once. The heating capacity is 40-80t/h, and the side-in and side-out, single-row fabrics meet the requirements of 50,000-300,000 tons of rolled products per year. The size of the crucible in the heating furnace is 6.6X24m.
16 rolling mills are adopted, and they are divided into three units of rough rolling, intermediate rolling and finishing rolling to form a full continuous rolling production line. The layout type is 6+6+4, and the main drive of the rolling mill adopts full digital PLC control. The roughing and intermediate rolling adopt the micro-tension continuous rolling, and a side loop is in the middle of the intermediate rolling and finishing rolling. The finishing mill has a vertical loop between each rolling mill to form tensionless and torsionless rolling. The maximum speed of the rolling mill can reach 5-16m/s.
There are 3 flying shears on the rolling line, which are located behind the three units and used for cutting heads, accidental breaks, and finished multiples. The shearing machine structure is a crank type, a rotary type, and a crank type combination.
Rolling process: 6.5mm disk diameter, 8-32mm rebar. The annual output of 50,000-300,000 tons rebar and wire rod production line requires 330,000 tons of continuous casting billet, and the comprehensive yield rate is 98% (negative deviation is considered).
The controlled rolling water-passing cooling device is arranged in front of the finishing mill, and the controlled cooling water-passing device is arranged after the finishing rolling mill to produce high-strength bar (three-stage steel) to improve the mechanical properties of the product.
The finishing collection area uses semi-automatic packaging equipment and 50 tons of cold shears.
The control system adopts computer secondary control and is divided into four zones (heating furnace zone, rolling zone, controlled cooling zone, and finishing zone), and each control point is dispersed and centralizedly controlled.